Die Metallverarbeitung war schon immer das Rückgrat der industriellen Produktion und befindet sich in einem tiefgreifenden Wandel. Präzision gewinnt an Schärfe, die Stückkosten sollen stets sinken, und Maschinen agieren längst intelligenter als reine Werkzeuge. Digitale Steuerungen, vernetzte Fräszentren und lernende Systeme verschieben Grenzen. Zudem trifft die moderne CNC-Bearbeitung auf smarte Robotik und KI. Dieser Artikel zeigt auf, wie neben der Vernetzung von Maschinen und Technologien, die Metallbearbeitung sich weiterentwickelt, stets mit dem Ziel zur nachhaltigen Hochpräzisionsfertigung der Zukunft.
Autor: Thomas W. Frick (LinkedIn-Profil / Xing-Profil)
Die Produktion läuft nachts, ohne Pause, während Sensoren Verschleiß erkennen und Parameter anpassen. Fabrikgelände werden leiser, Prozesse schneller, Ausschuss seltener. Wer die Technologien versteht, hat einen Vorsprung. Der Fortschritt ist schnell und passiert jetzt.
CNC-Bearbeitung im Flow
Fertigungsstätten verändern ihr Gesicht. Wo früher geschickte Hände Werkstücke formten, übernehmen heute Maschinenparks, die nicht nur zerspanen, sondern denken. CNC-Bearbeitung hat sich längst von der reinen Steuerungstechnik zu einem Echtzeit-Datenzentrum entwickelt. Prozesse laufen nicht mehr starr nach Vorgabe, sondern passen sich dynamisch an, Millimeterarbeit mit Köpfchen. Fünf-Achs-Fräsen drehen und schwenken Werkstücke wie von selbst, komplexe Geometrien entstehen in einem Zug. HSC-Bearbeitung bringt Geschwindigkeit ins Spiel, Spindeln jagen auf Höchsttouren, ohne dass die Genauigkeit leidet. Adaptive Vorschubregelung erkennt Materialwiderstände und justiert Vorschub permanent nach, Tools halten länger, Oberflächen glänzen. CAM-Software steuert den Ablauf nicht mehr bloß, sie verschmilzt mit der künstlichen Intelligenz in der Produktion. Werkzeugwege optimieren sich während der Bearbeitung, Standzeiten verlängern sich beinahe nebenbei. Maschinen senden Daten in die Konstruktion, Fehlerbilder fließen zurück in die Planung. Qualitätskontrolle rückt näher an den Span, Ausschuss sinkt, Nacharbeit verliert an Bedeutung.
Moderne CNC-Bearbeitung verändert nicht nur Maschinen, sie verändert, wie über Präzision gedacht wird. Der klassische Werkzeugkasten mag seinen Platz behalten, doch Zukunft gehört der digital gesteuerten Perfektion, die Werkhallen von Grund auf neu definiert.
Smart Factories und Fräsmaschinen heute
Fräszentren arbeiten längst nicht mehr isoliert, sondern als Teil modularer Systeme, die sich flexibel an Produktionsaufgaben anpassen. Bauteile unterschiedlicher Größe, Materialstärken und Toleranzen laufen über dieselbe Anlage, ohne dass komplizierte Umrüstzeiten den Fluss bremsen. Anlagen fahren mannlose Nachtschichten, während Roboterpaletten beladen und Werkstücke entgraten. Die Fertigung endet nicht mehr am Feierabend, sie läuft einfach weiter.
Spindelbelastung, Vibrationen, Temperatur, jede Bewegung wird erfasst. Sensorik greift ein, Maschinen reagieren, bevor Material nachgibt oder Werkzeuge stumpf werden. Schnittgeschwindigkeit reduziert sich, Vorschub zieht an, Kühlschmierstoff fließt bedarfsgerecht. Abweichungen verpuffen, Standzeiten verkürzen sich, Qualität bleibt stabil.
Predictive Maintenance verändert Stillstand zu einem planbaren Moment. Verschleiß kündigt sich nicht mehr überraschend an, sondern meldet sich rechtzeitig an. Maschinen stoppen nicht unvermittelt, Techniker stehen bereits bereit, Bauteile liegen auf Lager. Reparaturen werden integriert, Ausfälle verschwinden fast völlig.
Maschinen übermitteln Bearbeitungszeiten, Materialverbrauch und Energiebedarf direkt an die Steuerungsebene. ERP-Systeme greifen die Daten auf und sorgen dafür, dass Auftragsbücher sich anpassen und die Fertigungsplanung Ressourcen verschiebt. Stromspitzen werden vermieden, Leerlaufzeiten entfallen, Ausschuss reduziert sich spürbar.
CNC-Fräsanlagen arbeiten modular und vereinen präzise Steuerungstechnik mit digitaler Überwachung. Fräszentren integrieren sich in Produktionsumgebungen und stehen für den Wandel zur smarten Fabrik.
Leseempfehlung: Im Rahmen unserer Recherche, sind wir auf ein interessantes Fräsmaschinen-FAQ des Herstellers Knuth aufmerksam geworden, das zeigt wie solche Systeme funktionieren.
Lösungen entstehen, die Flexibilität und Effizienz verbinden. Werkhallen werden leiser, Abläufe glatter, Effizienz greift auf allen Ebenen. Smart Factories sind kein Zukunftsbild, sie formen längst den Alltag in der Zerspanung.
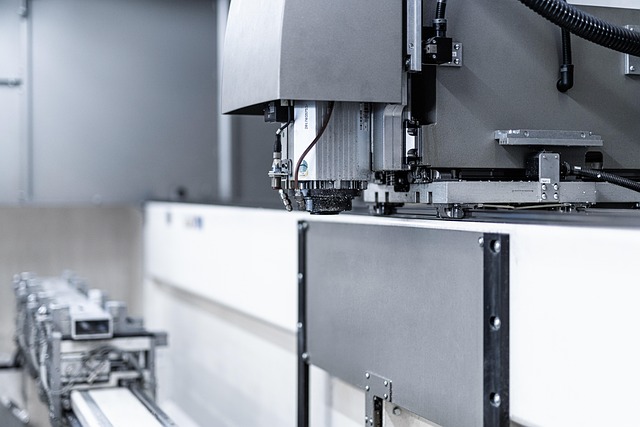
Robotik in der Zerspanung
Wo früher händisch be- und entladen wurde, greifen heute automatisierte Arme nach Rohlingen, entnehmen fertige Bauteile, entgraten Kanten und prüfen Oberflächen auf Makel. Cobots, die kollaborativen Roboter, stehen direkt neben Menschen. Schutzgitter verschwinden, Sicherheit entsteht durch Sensorik. Greifer reichen Teile weiter, ohne zu blockieren. Handlungsaufgaben lassen sich morgens noch anpassen, mittags bereits anders abarbeiten. Produktion bleibt beweglich, Fertigungslinien atmen.
Fräsen, Bohren, Schweißen verschmelzen in einer Station und machen Einzelbearbeitung zur Gesamtlösung. Hybride Zellen treiben diese Entwicklung voran. Werkstücke wandern, nicht mehr zwischen Arbeitsplätzen hin und her. Produktionsketten verkürzen sich, Logistikwege verschwinden, Bauteile verlassen die Maschine fertig.
Dünnwandige Bleche bleiben formstabil, empfindliche Aluminiumprofile lassen sich sicher bewegen, selbst komplexe Gussteile geraten nicht mehr ins Wanken. Greiftechnik hebt Grenzen auf. Fertigung, die lange als Handarbeit galt, wird jetzt vollautomatisch abgewickelt.
Nachhaltigkeit und Effizienz
Nachhaltigkeit und Effizienz bestimmen zunehmend die Ausrichtung der Metallbearbeitung. Produktionshallen verändern sich, Prozesse werden hinterfragt, Materialien effizienter genutzt. Einsparungen sind längst nicht mehr nur Kostenthema, sondern folgen dem Druck nach umweltfreundlicher Fertigung.
Kühlschmierstoffe auf Wasserbasis ersetzen klassische Öle, Trockenbearbeitung verzichtet vielerorts komplett auf Schmiermittel. Fertigung wird sauberer, Abfälle sinken, Entsorgungskosten fallen. Recycling rückt enger an den Prozess. Späne aus Aluminium, Titan oder anderen Legierungen landen nicht mehr im Container, sondern fließen direkt in Wiederaufbereitungsanlagen ein. Werkstoffe kehren in den Kreislauf zurück, Rohstoffverbrauch sinkt.
Hätten Sie das gedacht? Nach Angaben der Klimaschutz- und Energieagentur Niedersachsen arbeiten moderne Elektromotoren rund 40 % effizienter als ältere Modelle.
Der Energieverbrauch sinkt spürbar, ohne dass die Leistung nachlässt. Intelligente Steuerungen regulieren den Energiebedarf dynamisch und passen ihn an Werkstoff sowie Bearbeitungsprozesse an. In Pausenphasen drosseln Motoren automatisch ihre Leistung, wodurch der Verbrauch präzise auf den aktuellen Bedarf abgestimmt wird.
Luft- und Raumfahrt treiben den Wandel zusätzlich voran. Leichtbau bleibt dort Pflicht, jedes Gramm zählt. Mikrozerspanung ermöglicht filigrane Bauteile mit minimalem Materialeinsatz. Weniger Rohstoff, weniger Gewicht, weniger Energie – Einsparung auf jeder Ebene.
Metallbearbeitung wandelt sich vom reinen Zerspanen hin zur ressourcenschonenden Präzisionsarbeit. Effizienz bedeutet nicht nur schneller oder günstiger, sondern auch bewusster. Umwelt und Betrieb profitieren gleichermaßen, während die Branche nachhaltige Lösungen zur Norm erklärt.
Auf dem Laufenden bleiben
Mit einer Anti-Spam-Garantie und dem kostenlosen Informationsservice informieren wir Sie, gemäß Ihrer Themenauswahl kompakt über weitere Projekt- und Praxisbeispiele. Wählen Sie hierzu einfach Ihre Interessen und Themen aus: https://www.industrie-wegweiser.de/infoservice/
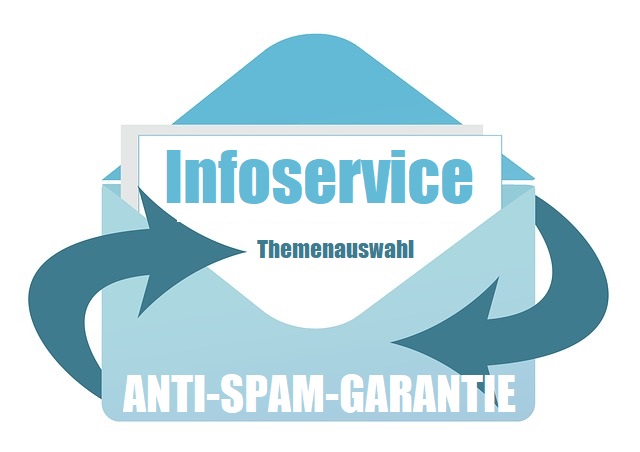
Kommentar hinterlassen zu "Metallverarbeitung heute und morgen"