Die Textilien, die heute etwa in der Kleidungsproduktion zum Einsatz kommen, haben kaum mehr etwas mit den Stoffen vergangener Tage zu tun. Ständig ist die Textilindustrie bemüht, noch innovativere und gleichzeitig nachhaltigere Stoffe zu produzieren. Ein Verfahren, das im Sinne dieser Bemühungen einen wichtigen Schritt darstellt, ist das N-Methylmorpholin-N-Oxid-Spinnverfahren. Dieses präsentiert sich als eine umweltschonendere Alternative zu den traditionellen Viskosespinnverfahren. Beim klassischen Verfahren und auch beim NMO-Spinnverfahren kommt den Spinndüsen eine besondere Rolle zu.
Die nachhaltigere Alternative dank NMO
Das klassische oder traditionelle Viskosespinnverfahren ist weltweit verbreitet, doch es steht wegen der Notwendigkeit chemischer Lösungsmittel in der Kritik. Das NMO-Spinnverfahren stellt hier insofern eine Verbesserung dar, als nicht mehr länger auf umweltschädliche Lösungsmittel zurückgegriffen werden muss. N-Methylmorpholin-N-Oxid, oder NMO, ist ein organischer Stoff und ungiftig. Dieser Stoff löst den Zellstoff auf, bevor dieser mittels der Spinndüsen in Form gebracht wird. Das NMO-Spinnverfahren ist ein geschlossener Kreislauf, sodass eine annähernd vollständige Rückgewinnung und Wiederverwendung des NMO möglich sind. Das stellt einen weiteren Schritt zur Reduzierung der Umweltbelastung und zu deutlichen Einsparungen in der Industrie dar.
Welche Rolle kommt den Spinndüsen zu?
Unabhängig davon, ob sich Hersteller am NMO-Spinnverfahren versuchen oder auf die klassische Methode setzen, spielen die Spinndüsen eine tragende Rolle. Bei einer Spinndüse handelt es sich um ein erstaunliches Präzisionsbauteil, das sich durch seine exakt gefertigten, winzig kleinen Öffnungen, auszeichnet. Die vorher gelöste Zellulosemasse wird unter hohem Druck in die Düsen gepresst, was zur Entstehung feinster Fäden führt. Die Machart und die Beschaffenheit der Düsen entscheiden letztlich über die Art und das Erscheinungsbild des fertigen Gewebes. Wie fest, fein oder wie glänzend ist dieses? Viele dieser Faktoren entscheiden sich bereits durch die eingesetzte Düse.
Beim NMO-Spinnverfahren stellen die Eigenschaften des umweltschonenden Lösungsmittels spezielle Anforderungen an die Düsen. Entscheidend ist, dass sie dem organischen Lösungsmittel gegenüber resistent sind und gleichzeitig dauerhaft eine gleichmäßige und präzise Fadenbildung garantieren. Aufgrund der Komplexität der Spinndüsen erfordert deren Entwicklung und Fertigung ein spezielles Know-how. Ein Unternehmen, das sich in diesem Bereich hervorgetan hat und heute als Weltmarktführer gilt, ist die Elmer GmbH aus Österreich. Seit Jahren entwickelt das innovative Unternehmen Spinndüsen für modernste Fertigungstechnologien. Die konstante Weiterentwicklung des Unternehmens fördert den Umstieg auf nachhaltige Methoden.
Viskosefasern – praktisch überall im Einsatz
Viskosefasern lassen sich vielerorts im alltäglichen Leben finden, unabhängig von der Art ihrer Fertigung. Was die Viskose seit jeher auszeichnet, sind ihre Saugfähigkeit, der seidige Glanz und der weiche Griff. Verständlicherweise findet das Material breite Anwendung in der Textilindustrie. Ebenso kommen Viskosefasern auch bei technischen Anwendungen zum Einsatz, etwa in verschiedenen Filtern oder in Fasern, die der Verstärkung eines Trägermaterials dienen.
Neue Technik und die Bereitschaft für Veränderungen
Unternehmen wie der Weltmarktführer für Spinndüsen, ermöglichen es der Textilbranche durch stetige Weiterentwicklung und zukunftsweisende Forschung, einfacher, schneller und günstiger, umweltschonendere Verfahren in die bestehenden Prozesse zu integrieren. Das NMO-Spinnverfahren kann die Umweltbelastung drastisch reduzieren, doch die Qualität der Viskose bleibt gleich. Viskose ist weiterhin in etlichen Branchen ein gefragtes Material, sodass die Förderung des NMO-Spinnverfahren die richtige Entscheidung für eine lebenswertere und gesündere Zukunft ist.
Grundlegender Prozessablauf für das Spinnen
Der Prozess des Spinnverfahrens beginnt mit der Materialvorbereitung. In diesem Prozessschritt finden folgende Arbeitsvorgänge statt:
- Rohstoffe auswählen, mit der beispielhaften Fragestellung, ob natürliche oder synthetische Fasern?
— - Nach dem Wareneingang des Rohmaterials muss eine gründliche Reinigung und danach die Trocknung des Rohmaterials erfolgen.
— - Farbstoffe, Stabilisatoren und Weichmacher, werden je nach gewünschter Eigenschaft, gemischt.
Ein weiterer zentraler Prozessschritt ist das Schmelzen und Lösen von Materialien. Beim Nass- oder Trockenspinnen werden mit einem Lösungsmittel Materialien aufgelöst. Beim Schmelzspinnen werden die Rohstoffe erhitzt bis diese schmelzen. Ebenso wird in dieser Phase durch Filtrieren und Rühren die Qualität einer homogenen Masse sichergestellt.
Der eigentliche Spinnvorgang beginnt mit der Extrusion, indem die vorbereitete Masse durch Spinndüsen gepresst wird. Im darauffolgenden Arbeitsgang werden die extrudierten Filamente je nach Verfahren, getrocknet oder gekühlt. Um die Festigkeit zu erhöhen und sich an der Molekularstruktur auszurichten, werden die Filamente gestreckt.
Im Nachbehandlungsprozess werden die Filamente mittels chemischer und physikalischer Verfahren gehärtet. Beim Nasspinnen mittels Koagulation und beim Trockenspinnen mittels Trocknung. In dieser Phase finden auch optionale Oberflächenbehandlungen statt, wie z.B. die Verbesserung der Haftung.
Vor der Weiterverarbeitung und Einlagerung erfolgt die Qualitätssicherung und das Aufspulen. Nach der Überprüfung der Festigkeit und Gleichmäßigkeit, werden die Filmente auf Spulen aufgerollt und somit die Weiterverarbeitung, Einlagerung und der Transport vereinfacht.
Auf dem Laufenden bleiben
Mit einer Anti-Spam-Garantie und dem kostenlosen Informationsservice informieren wir Sie, gemäß Ihrer Themenauswahl kompakt über weitere Projekt- und Praxisbeispiele. Wählen Sie hierzu einfach Ihre Interessen und Themen aus: https://www.industrie-wegweiser.de/infoservice/
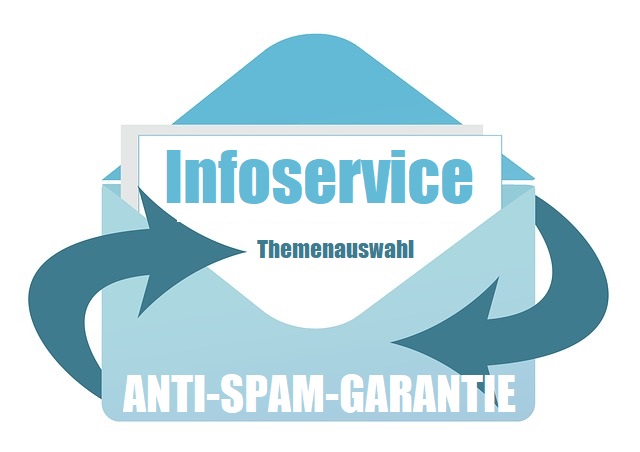
Kommentar hinterlassen zu "Das NMO-Spinnverfahren als nachhaltige Alternative erklärt"