Fehleranalysen sind wichtig, da Fehler und Probleme rund um ein Produkt und dessen Produktion nicht nur ärgerlich sind, sondern einen hohen finanziellen Schaden anrichten können und zusätzlich das Image des Unternehmens schädigen. Die sogenannte Fehlermöglichkeitsanalyse FMEA dient dazu, Fehler frühzeitig und konsequent vorzubeugen. Um was es dabei genau geht, wie die FMEA in der Praxis aussieht und welche konkreten Vorteile sie mit sich bringt, erläutert der folgende Artikel mit Beispielen.
FMEA Kurznavigation
Autor: Thomas W. Frick (LinkedIn-Profil / Xing-Profil)
Was ist FMEA?
In den 60er Jahren suchte die NASA nach einer Möglichkeit, die Sicherheitsrisiken des Apollo-Projekts einschätzen und minimieren zu können. Zu diesem Zweck entwickelte die Raumfahrtbehörde schließlich die FMEA. Das Kürzel FMEA steht für:
- Failure
- Mode and
- Effects
- Analysis,
zu Deutsch „Fehlermöglichkeits- und Einflussanalyse“. Das Projekt war von Erfolg gekrönt. Es zeigte sich, dass es die Methode ermöglichte, kleine Fehler, die zu großen negativen Auswirkungen führen können, zuverlässig zu identifizieren. Die FMEA etablierte sich in den folgenden Jahrzehnten als angesehenes Instrument zur Qualitätssicherung, das vor allem von der Automobilindustrie eingesetzt und weiterentwickelt wurde. Seit 1980 ist die Methode in Deutschland genormt und kommt zunehmend auch in anderen Branchen zum Einsatz.
Hinweis: Unsere Berichte sind oft sehr ausführlich. Daher bieten wir den FMEA-Analyse Download, eine Zusendung des Artikels im PDF-Format zur späteren Sichtung an. Nutzen Sie das Angebot um sich die Praxis-Impulse in Ruhe durchzulesen, Sie können hierfür auch einfach auf das PDF-Symbol klicken.
Was sind die Ziele der FMEA-Analyse?
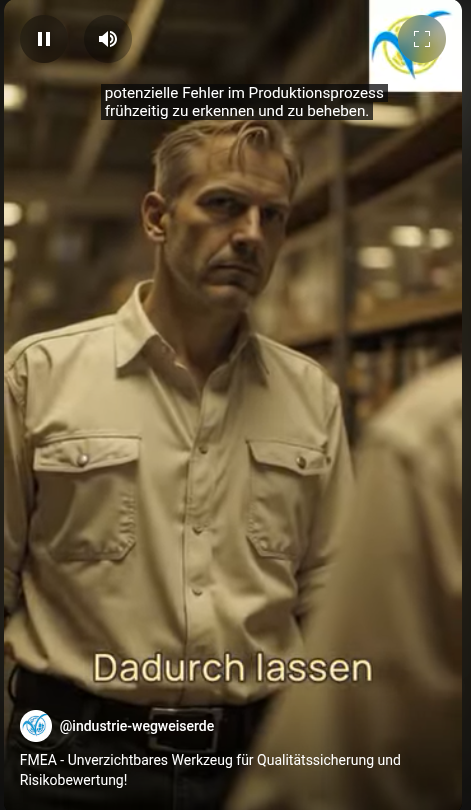
Ziel ist es, potenzielle Fehlermöglichkeiten frühzeitig zu identifizieren und durch systematische Maßnahmenanalyse das Risiko für den Kunden zu minimieren. Dabei helfen standardisierte Formblätter, um alle relevanten Informationen strukturiert festzuhalten. Die Vorgehensweise beginnt mit einer Strukturanalyse, bei der das Gesamtsystem in logisch zusammenhängende Komponenten gegliedert wird. Diese Logik bildet die Grundlage für alle weiteren Analysen innerhalb der FMEA. Die Fehlermöglichkeits- und Einflussanalyse ist ein bewährtes Instrument zur Risikobewertung technischer Systeme und Prozesse.
Welche Vorteile entstehen durch die FMEA?
Im Detail gehen mit der FMEA folgende Vorteile einher:
1. Fehlererkennung in der Testphase
Wird die Fehlermöglichkeits- und Einflussanalyse frühzeitig, korrekt und lückenlos durchgeführt, lassen sich Fehler am Produkt oder im Produktionsprozess erkennen und beheben, bevor sie weitreichende Auswirkungen nach sich ziehen können. Bereits in der Testphase zeigt sich, welche möglichen Fehlerquellen bestehen und wie diese beseitigt werden können.
2. Vermeidung von Folgekosten
Auch kleine Fehler können viel Schaden anrichten und zu hohen Folgekosten führen. Werden die Fehler aber frühzeitig erkannt und ausgemerzt, ist dies mit vergleichsweise minimalem finanziellen Aufwand möglich.
3. Vorbeugen von Imageschäden
Im schlimmsten Fall fällt der Fehler nicht dem Unternehmen, sondern dem Kunden auf. In der Folge erleidet das Unternehmen einen Imageschaden und riskiert, die betroffenen Kunden unwiderruflich zu verlieren. Das Risiko, dass es zur erstmaligen Fehlererkennung durch den Kunden kommt, lässt sich mit der FMEA drastisch reduzieren.
4. Steigerung der Produktqualität
Letztendlich führt die Fehlermöglichkeits- und Einflussanalyse zu einer spürbar gesteigerten Produktqualität.
Die drei Phasen der FMEA
Grundsätzlich lässt sich die Methode in drei Phasen unterteilen:
System-FMEA
Die System-FMEA zielt darauf ab, ein hochfunktionales und sicheres System zu erschaffen oder zu erhalten. Im Rahmen der Analyse werden Pflichtenhefte und Systemkonzepte erarbeitet und die einzelnen Komponenten des Systems auf ihr Zusammenspiel, ihre Funktionalität und ihre Sicherheit überprüft.
Konstruktions-FMEA
Die Konstruktions-FMEA baut auf die bestehenden Konstruktionspläne auf. Diese werden genauestens analysiert und hinsichtlich möglicher Fehlerquellen und Ausfallrisiken der einzelnen Bauteile untersucht.
Prozess-FMEA
Die Prozess-FMEA bezieht sich auf die Produktionsprozesse, deren Eignung und Qualität. Ausgehend von den vorliegenden Fertigungsplänen werden mögliche Produktionsfehler ausgemacht. Das Hauptaugenmerk liegt auf der Zuverlässigkeit und optimalen Eignung des gesamten Produktionsprozesses.
In aller Regel werden die drei Phasen nicht einzeln, sondern aufeinander aufbauend eingesetzt. Auf die Überprüfung des großen Ganzen – also des Systems – folgt die Analyse der Konstruktion und schließlich die Prozessanalyse. In Einzelfällen kann es allerdings Sinn ergeben, die Reihenfolge umzukehren, sämtliche FMEA-Arten parallel laufen zu lassen oder sich lediglich auf ein bis zwei Schritte zu konzentrieren.
Hinweis: Unsere Berichte sind oft sehr ausführlich. Daher bieten wir den FMEA-Analyse Download,eine Zusendung des Artikels im PDF-Format zur späteren Sichtung an. Nutzen Sie das Angebot um sich die Praxis-Impulse in Ruhe durchzulesen, Sie können hierfür auch einfach auf das PDF-Symbol klicken.
Wie funktioniert die FMEA in der Praxis?
FMEA ist Teamarbeit. Mitarbeiter aus den Bereichen Entwicklung, Konstruktion, Fertigungsplanung und -ausführung sowie Qualitätsmanagement müssen Hand in Hand zusammenarbeiten, um eine erfolgreiche und wirklich ergebnisbringende Fehlermöglichkeits- und Einflussanalyse durchzuführen. Damit die Ergebnisse und Erkenntnisse später übersichtlich und nachvollziehbar vorliegen, müssen Formblätter oder geeignete Softwares genutzt werden. Schritt für Schritt läuft eine FMEA in der Praxis vereinfacht dargestellt folgendermaßen ab:
Schritt 1: Bestimmung des Fehlerortes
Im ersten Schritt werden mögliche Fehlerorte ausgemacht. An welchen Stellen könnte sich eine Fehlerquelle befinden? Frühere Erfahrungen und spezielle Fachkenntnisse der einzelnen Beteiligten helfen dabei, relevante Fehlerorte zu bestimmen.
Schritt 2: Definition des Fehlers
Steht ein möglicher Fehlerort fest, gilt es, den Fehler zu definieren.
- Um welche Art von Fehler handelt es sich?
- Und wie genau gestaltet sich dieser Fehler?
Schritt 3: Zuordnen einer Priorität
Dann wird eingeschätzt, welches Risiko für das Unternehmen mit diesem Fehler einhergeht. Basierend darauf wird dem Fehler eine Risikoprioritätszahl (RPZ) zugeordnet. Diese ergibt sich aus den Faktoren
- Auftrittswahrscheinlichkeit,
- Bedeutung und
- Entdeckungswahrscheinlichkeit.
Durch die Multiplikation dieser Werte entsteht eine klare Priorität für jede identifizierte Fehlerursache. Je höher die RPZ, desto dringender sind präventive oder korrektive Entdeckungsmaßnahmen erforderlich. Die Anwendung der RPZ folgt dabei einer nachvollziehbaren Logik, die sowohl in der AIAG- als auch in der VDA-Methodik verankert ist. Durch die Risikoprioritätszahl (RPZ) wird ersichtlich, welche möglichen Fehler zuerst bearbeitet werden müssen und welche eher zweit- oder drittrangig zu beachten sind.
Die Entdeckungswahrscheinlichkeit spielt bei allen FMEA-Formen eine entscheidende Rolle, da sie angibt, wie gut ein Fehler mit den vorhandenen Prüfmethoden erkannt werden kann. Kombiniert mit der Auswirkungsanalyse ergibt sich eine robuste Basis für die Risikobewertung und die Ableitung gezielter Entdeckungsmaßnahmen. Die Genauigkeit dieser Einschätzungen hängt stark von der gewählten Betrachtungstiefe und der Erfahrung des Teams ab. Ein gut geführtes Formblatt, das auf das jeweilige Gesamtsystem angepasst ist, sorgt für Transparenz und Nachvollziehbarkeit.
Schritt 4: Identifikation der Fehlerursache
Im Anschluss setzen die Beteiligten ihr Know-how ein, um der Fehlerursache auf den Grund zu gehen.
Schritt 5: Sammeln von Lösungsvorschlägen
Ist die Ursache des jeweiligen Fehlers bekannt, werden Lösungsvorschläge zur Vermeidung und Behebung des Fehlers gesammelt.
Schritt 6: Vermeidung des Fehlers
Zu guter Letzt werden konkrete Maßnahmen festgelegt, mit denen der Fehler in der Realität vermieden oder behoben werden kann.
Welche Beispiele gibt es für die FMEA-Analyse?
Prozess-FMEA – Beispiel aus der Autoproduktion (Schweißen einer Karosserie)
Element | Möglicher Fehler | Fehlerfolge | Fehlerursache | Maßnahme |
---|---|---|---|---|
Schweißroboter | Schweißnaht unvollständig | Instabile Karosserie, Reklamation | Roboter falsch programmiert | Schulung, regelmäßige Prüfungen |
Werkstückpositionierung | Bauteil nicht korrekt fixiert | Schweißposition fehlerhaft | Positioniersystem defekt | Wartung verbessern, visuelle Kontrolle |
Energie-versorgung | Spannungs-einbruch | Schweißpunkt nicht ausgeführt | Leitung defekt oder lose | Wartungsintervall verkürzen |
Design-FMEA Beispiel – Elektrischer Wasserkocher
Element | Möglicher Fehler | Fehlerfolge | Fehlerursache | Maßnahme |
---|---|---|---|---|
Thermostat | Schaltet nicht ab | Überhitzung, Brandgefahr | Kontaktproblem | Thermostat-qualität prüfen |
Heizspirale | Korrosion | Heizt nicht mehr, Kurzschluss | Materialfehler, Kalkablagerung | Material ändern, Entkalkungs-hinweis |
Gehäuse | Wird zu heiß außen | Verbrühungsgefahr für Nutzer | Schlechte Isolierung | Doppelschicht-Gehäuse einsetzen |
Beispiel aus der Medizin – Prozess-FMEA für Medikamentenabgabe im Krankenhaus
Element | Möglicher Fehler | Fehlerfolge | Fehlerursache | Maßnahme |
---|---|---|---|---|
Medikamentenvergabe | Falsche Dosis verabreicht | Gesundheits-gefahr für den Patienten | Ablesefehler, Verwechslung | Barcode-Scan-System, Doppelkontrolle |
Verabreichungszeit | Medikament verspätet gegeben | Wirkung reduziert, Therapie verzögert | Zeitplanfehler | Automatische Erinnerungen, QM-Kontrolle |
Dokumentation | Nicht dokumentiert | Rückverfolgung unmöglich | Zeitmangel, Systemausfall | Elektronische Patientenakte verwenden |
Wie bekam die FMEA-Analyse eine internationale Bedeutung?
Durch die Normen und Empfehlungen von AIAG und VDA haben die FMEA international harmonisiert. Beide Organisationen legen besonderen Wert auf die gemeinsame Analyse von Fehlerkette, Fehlermöglichkeiten und den daraus resultierenden Risiken. Während AIAG traditionell stärker auf die Automobilzulieferer in den USA ausgerichtet ist, bringt VDA die Perspektive der deutschen Automobilindustrie ein. Im Fokus steht dabei immer die Verbesserung der Betrachtungstiefe sowie die Effizienz der Entdeckungsmaßnahmen entlang des Produktentwicklungsprozesses.
FMEA Weiterentwicklung und Vertiefung
Auch eine bewährte Methode, die über Jahrzehnte hinweg seine Praxistauglichkeit unter Beweis gestellt hat, unterliegt dem Wandel und muss regelmäßig angepasst und erweitert werden. In diesem Zusammenhang stössst man auf weitere Fachbegriffe, welche wir kompakt erläutern möchten:
Worin unterscheiden sich FMEA und FMECA?
FMECA steht für Failure Modes, Effects, and Criticality Analysis. Es handelt sich dabei um eine erweiterte Form der Fehlermöglichkeits- und Einflussanalyse. Während die FMEA sich auf die Identifizierung von möglichen Fehlern, ihrer Ursachen und potenziellen Auswirkungen konzentriert, geht die FMECA einen Schritt weiter und integriert auch die Bewertung der kritischen Bedeutung dieser Fehler. In einer FMECA werden nicht nur die Wahrscheinlichkeit und die Auswirkungen eines Fehlers bewertet, sondern auch die kritische Bedeutung dieses Fehlers für das Gesamtsystem oder den Prozess. Dies umfasst eine Analyse der möglichen Konsequenzen auf die Sicherheit, die Produktion, die Umwelt oder andere kritische Aspekte.
Besonders in sicherheitskritischen Branchen kommen FMECA und FMEDA zum Einsatz. Diese Methoden beinhalten zusätzlich zur Ausfalleffektanalyse eine vertiefte Risikobewertung, die vor allem auf quantitative Daten setzt. Besonders in der Elektronikentwicklung erlaubt die FMEDA eine genauere Fehlernetz-Darstellung, in dem Fehlermöglichkeiten, Fehlerfolge und deren Auftretenswahrscheinlichkeit in Beziehung gesetzt werden. So kann das Gesamtsystem auf seine Zuverlässigkeit geprüft und Schwachstellen systematisch adressiert werden.
Beispiele für den Einsatz: Die FMECA wird häufig in sicherheitskritischen Branchen wie der Luft- und Raumfahrt, der Verteidigung und der Medizintechnik eingesetzt, um sicherzustellen, dass potenzielle Fehler und Risiken umfassend bewertet werden.
Was ist der Unterschied zur FMEDA?
FMEDA steht für Failure Modes, Effects, and Diagnostic Analysis. Es handelt sich um eine spezifische Form der Fehleranalyse, die neben den Fehlermodi und ihren Auswirkungen auch die Fähigkeit eines Systems berücksichtigt, diese Fehler zu diagnostizieren. In einer FMEDA werden die möglichen Fehler eines Systems, ihre Auswirkungen und die Wahrscheinlichkeit ihrer Entdeckung analysiert. Diese Methode ist besonders relevant in sicherheitskritischen Anwendungen, in denen nicht nur die Vermeidung von Fehlern, sondern auch die Fähigkeit zur frühzeitigen Erkennung und Diagnose von Fehlern entscheidend ist.
Beispiele für den Einsatz: Die FMEDA wird oft in der Entwicklung von elektronischen Systemen, insbesondere in der Automobilindustrie und anderen Branchen mit hohen Sicherheitsanforderungen, angewendet.
Welche weitere Formen der FMEA-Analyse gibt es?
Spezielle Formen wie DFMEA (Design-FMEA) und DRBFM (Design Review Based on Failure Mode) erweitern die klassische FMEA. Die DFMEA konzentriert sich auf potenzielle Schwächen im Konstruktionsprozess, wohingegen DRBFM auf Änderungen im Design und deren mögliche Fehlerfolge fokussiert. Beide Methoden zielen darauf ab, eine frühzeitige Einflussanalyse durchzuführen, um gefährliche Fehlerursachen vor der Serienfertigung zu beseitigen. Die Maßnahmenanalyse erfolgt dabei mit ähnlicher Logik wie bei der klassischen FMEA.
Welche Fehlerkosten können mittels einer FMEA-Analyse reduziert werden?
Folgende Fehlerkosten können mittels FMEA identifiziert und minimiert werden:
- Herstellungskosten, z.B. Ausschuss, Nacharbeit oder Produktionsausfälle, Kosten für zusätzliches Material und Arbeitszeit.
- Garantiekosten, z.B. Gewährleistungsansprüche und Reparaturkosten.
- Kundenreklamationen, z.B. Rückrufaktionen, Reparaturen oder Ersatzleistungen und Bearbeitunszeiten für Reklamationen.
- Rufschäden, z.B. langfristiger Imageschaden die das Ansehen eine Unternehmens, auch in Bezug auf die Nachhaltigkeit schädigen.
- Produktionsausfallkosten, Fehler und Probleme verursachen Stillstandszeiten, welche zur Erhöhung der Produktionskosten führen.
- Kosten für die Fehlererkennung und Korrekturen, z.B. Kosten für Tests, Inspektionen und Produktivitätssenkung im Entwicklungsprozess und Produktionsprozess.
- Regulatorische Strafen, z.B. gesetzliche Verstöße, Konventionalstrafen und Verzugskosten.
FMEA Zusammenfassung
Die Fehlermöglichkeits- und Einflussanalyse ist eine bewährte Methode zur Qualitätssicherung, um potenzielle Schwachstellen von Produkten frühzeitig zu erkennen und zu beheben. Im Mittelpunkt dieser Methode stehen die Risikoprüfziffern (RPZ). Die helfen dabei die Entdeckungsmaßnahmen und Fehlerfolgen zu priorisieren.
Die Beteiligung der Automotive Industry Action Group (AIAG) unterstreicht die Wichtigkeit und die Marktdurchdringung in der Industrie. Bewertungen von Fehlerursachen, Auftretenswahrscheinlichkeit und Bewertungszahlen bildet die Grundlage für eine präzise Risikobewertung. Weitere Firma und Organisationen haben die FMEA-Analyse erweitert, wie z.B. Toyota mittels dem Design Review Based on Failure Mode (DRBFM) oder der VDA mittels vielfältiger Bewertungskali.
Die jeweiligen Abstellmaßnahmen basieren auf durchgeführte Risikobewertungen, ergänzend bieten Bewertungskataloge eine Orientierung. Methodenbeschreibung und Handlungsbedarf leiten die Auswirkungsanalyse ein. FMCEA und FMEDA ermöglichen eine tiefgehende Fehleranalyse, während Teilprozesse und Systemelemente in die Gesamtbewertung einfließen.
Aufgabenpriorität und Ausfalleffektanalyse lenken den Fokus auf wichtige Aspekte. Die Vorgehensweise, Teammitglieder und Auftrittswahrscheinlichkeit beeinflussen die Umsetzung von FMEA. Die Integration in die Unternehmensziele schafft eine strategische Grundlage für erfolgreiche Fehlervermeidung.
Auf dem Laufenden bleiben
Mit einer Anti-Spam-Garantie und dem kostenlosen Informationsservice informieren wir Sie, gemäß Ihrer Themenauswahl kompakt über weitere Projekt- und Praxisbeispiele. Wählen Sie hierzu einfach Ihre Interessen und Themen aus: https://www.industrie-wegweiser.de/infoservice/
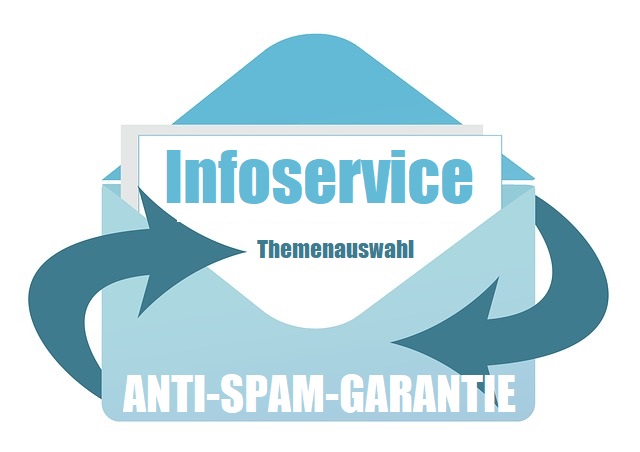
Kommentar hinterlassen zu "FMEA-Analyse zur Fehlermöglichkeits- und Einflussanalyse"